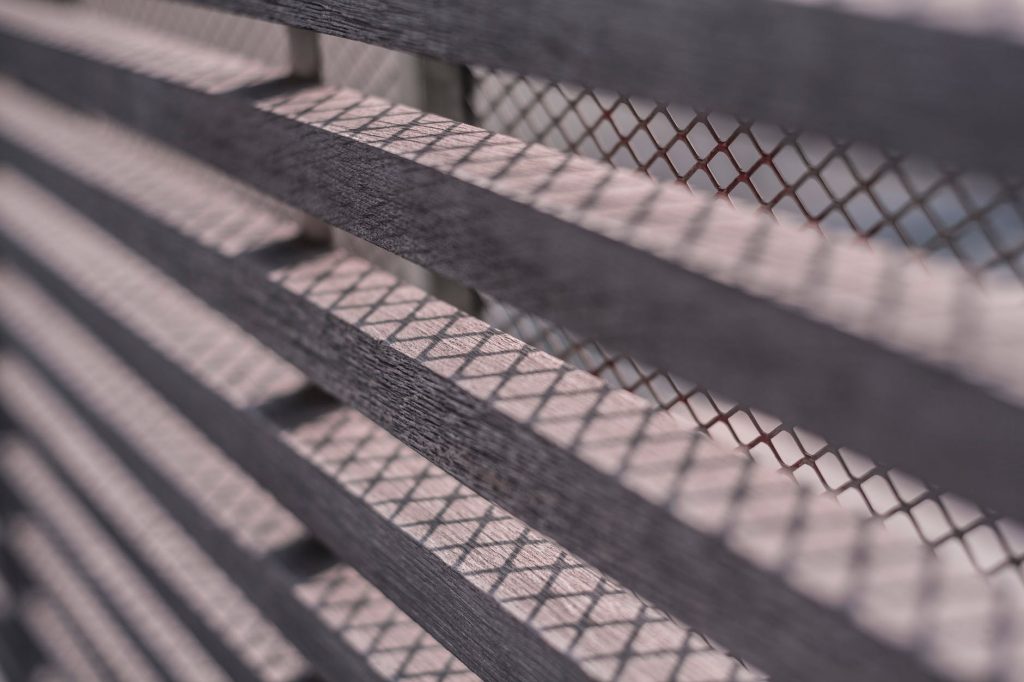
We will investigate how the two regular types of wire work are made. Welded mesh manufacturers can complete a scope of manifestations, for example, welded or woven work which will be examined beneath. A basic type of metal screen which includes parallel rows and meeting sections of wire is called wire mesh. These connecting wires are commonly united by welding or weaving – two of the more common types of wire mesh. The solid wire utilized is frequently made by continuously drawing down a metal in a series of round dies the bucket until it achieves the appropriate measurement. Although they are similar in appearance and their applications, perforated metal sheet and expanded metal sheet are not types of wire mesh. Wire mesh comes in an almost endless variety of shapes and sizes, and a broad combination of materials and metal compounds.
Welded Wire Work
Welded wire mesh has crossed lines and segments of parallel wires that are welded together at the meeting point. When the wire achieved the desired length, it is fed into a machine that welds various lines of wire along at their crossing point. As the mesh is fed through the machine, a parallel line of welds is then shaped at the same time where the opposite lines meet. The other intersection of wires after that point is being fed through the machine to be welded, and this process continues, turning it into a part of each line of wires as a whole. This instrument usually welds the wires using the electrical current as a source of heat. Despite the fact that other welding strategies could be utilized, this is the most economical way. Once the mesh has achieved the predefined length, it is cut by a shear that results in a sheet of a flat and strong welded wire work.
Woven Wire Mesh
Much the same as a woven textile, the woven wire mesh has an assortment range of crossing wires. Usually, the wires are woven over and under the opposite wires to make a strong sheet. This arrangement is called a ‘ Plain Weave Work’. While for applications that require a flexible sheet, a ’Twill Weave’ can be used. This includes a wire that is woven over a couple of opposite wires, at that point underneath ensuing arrangement of two opposite wires, and so on. Woven wire mesh doesn’t have welds on them. Instead, they are supported into a machine like a loom which strengthens a straight wire through the planned weave pattern. The wires are then bowed to the opposite position, and then the other straight wire is supplied through the pattern. The machine continues with this process until the predefined measurements are accomplished and the completed wire mesh sheet is cut into specific sizes.
We will investigate how the two normal types of wire mesh are shaped. Welded mesh manufacturers can complete a scope of concepts. For example, welded or woven mesh which will be talked about below. A regular type of metal screen which contains parallel columns and meeting sections of wire is called wire mesh. These connecting wires are commonly consolidated by welding or weaving – two of the more common types of wire work. The strong wire used is usually made by continuously drawing down a metal in a continuous of round dies the dust until it achieves the desired width. In spite of indistinguishable in appearance and their applications, perforated metal sheet and expanded metal sheet is not types of wire mesh. Wire mesh usually comes in an almost infinite measure of shapes and sizes, and a broad combination of materials and metal compounds.